According to Erick Soares, Senior Product Manager – UPS and Renewables, C&D Technologies, selecting the best battery for your data centre’s backup power system isn’t just a technical decision – it’s a strategic one.
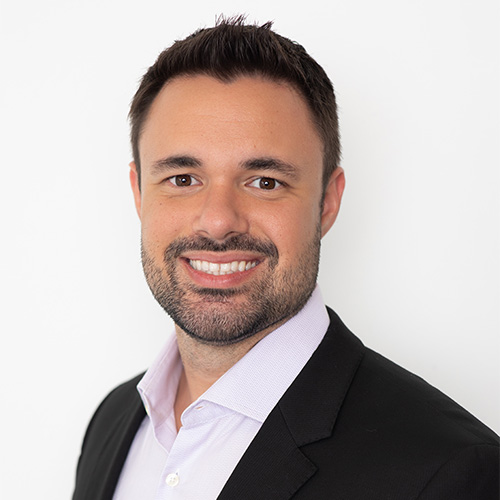
When selecting the most appropriate technology for a data centre battery backup power system it’s essential to look beyond what is available or trending. Each facility has its own unique aspects impacting the choice, determined by such factors as size, location, energy quality and availability, cooling performance and customer preference.
Crafting a reliable system means considering every variable to ensure maximum reliability and the highest return on investment (ROI). Every data centre is different, and every decision must align with these specific conditions.
Greenfield vs Brownfield projects: Tailoring your battery strategy
For new data centres (Greenfield projects), battery decision factors are more straightforward. With a blank canvas, it is much easier to plan proper ventilation, HVAC systems and fire suppression to support the desired technology.
However, new projects present a bigger challenge when it comes to capacity. Computational capacity, along with all backup systems required to support it, are based on predicted demand for the data centre’s life. With our crystal balls being cloudy at best, and thanks to huge increases in demand from AI, a data centre built five years ago may already be falling short today.
Brownfield projects — expansions or retrofits — present their own complexities. Rooms originally sized for a specific battery type or with certain design features may make it harder to accommodate newer technologies or support additional capacity. Room size, cooling/ventilation and fire suppression are some of the main factors that must be considered. This evaluation will serve as the basis to determine if it is better to maintain the existing technology, retrofit with a new one, or even build a new building from scratch.
The size factor: Why data centre dimensions matter for battery backup
The size of the data centre facility directly influences its power requirements, dictating the space available for servers and backup systems. Servers are revenue generators for a data centre while batteries and generators ensure continuity. Striking a healthy balance is crucial. While loads will fluctuate over time, it is important to design your backup systems with 100% load in mind to minimise any potential issues in the future.
To properly size your battery system, the actual or expected power requirements and time for depletion or discharge before generators or other backup power is required must be determined.
Another important decision factor for battery chemistry is the quality of power and frequency in which batteries will be used. Stable power will always be easier on the batteries, leading to longer life, while frequent hits (i.e. unstable power) will constantly drain the batteries, leading to a potentially shorter life.
From a physical perspective, space efficiency matters. Different designs impact how the batteries orient within the cabinets, racks, or containers factor into the overall footprint. Racks and connections vary based on battery system requirements. Certain battery systems require proprietary or purpose-built cabinets. Others can be stored in open racks or cabinets.
Top terminal batteries are more commonly available, while front terminal batteries are safer and more efficient. When considering front terminal batteries, it is recommended to select batteries (Figure 1) with ‘true’ front access in which there is a direct weld from the battery plates to the front access terminal of each monobloc. Other batteries that place the terminals through the top cover of the monobloc require additional connectors and brackets to deliver the same result, adding to the complexity and potential points of failure.
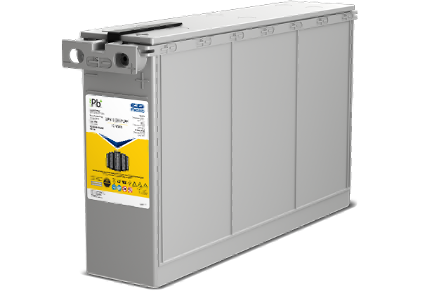
Figure 1: Batteries with ‘true’ front access are safer and more efficient than top terminal batteries.
Choosing the right battery chemistry: Performance, longevity and future-proofing
Flooded Lead Acid, Valve Regulated Lead Acid (VRLA) and Lithium-ion batteries are the three most used chemistries in today’s data centres, each with unique advantages and trade-offs. Both flooded and VRLA batteries are based on lead acid chemistry and use the same basic principle, albeit with very different intended results.
Flooded Lead Acid has been the trusted workhorse for decades, VRLA batteries have become the industry standard in the last 20-30 years thanks to a smaller footprint, lower required maintenance and the ability to be housed within the same space as servers. Lower costs are offset by a shorter lifespan compared to flooded batteries, so battery replacements need to be considered as part of the total cost of ownership (TCO) of a backup system.
Advancements in VRLA technology, particularly with pure lead and advanced pure lead designs, have dramatically extended their lifespan, with some models offering up to 10 years of reliable service. This evolution bridges the gap with Lithium-ion batteries, which have gained traction due to their longevity and performance in high-demand applications. Yet, Advanced Pure Lead (Figure 2) batteries offer a safer and more cost-effective alternative while still providing competitive life expectancy and performance.
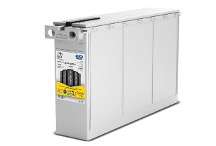
Figure 2: Advanced pure lead VRLA batteries can last as long as 10 years.
With the increased popularity of Lithium-ion, thanks to the wider adoption of electric vehicles, lead acid technology has been put under pressure to improve its life expectancy while still maintaining its safety and recyclability. Thanks to the development of advanced pure lead technology, it is now possible to match the life expectancy offered by Lithium-ion with the additional safety, recyclability and lower costs of lead acid technology.
Advanced pure lead – Why is it different?
Two key components are key to determining battery life: the grid and the paste. The paste generates the energy in the battery while the grids transfer energy to the terminals so it can be used. Due to normal operations of batteries, the grids will corrode, and the paste will dry out. The speed at which this happens is what will determine battery life.
Standard VRLA batteries use a mix of lead and other elements to achieve a good balance between cost and life. However, due to the presence of other elements, and a simpler manufacturing process, they are limited in terms of performance, heat tolerance and even storage time.
Pure lead batteries use higher purity materials (virgin lead), along with other manufacturing improvements to help reduce the rate of grid corrosion and paste dry-out. Thanks to these advancements, pure lead batteries have an extended life, increased runtime, prolonged storage time and improved heat tolerance. It’s important to note there isn’t a single way to make a pure lead battery, so every manufacturer will have a unique approach.
Building on the solid pure lead foundation, the advanced pure lead technology takes life expectancy closer to Lithium-ion by introducing a catalyst to further delay paste dry-out. While catalysts are not new to the industry, adding them to a 12V pure lead battery is, and it allows us to achieve the resulting 7-10-year life expectancy.
A future-focused strategy
By thoroughly understanding the different battery chemistries and their applications, you can make decisions to safeguard your operations and future-proof your investment and growing power demands. A comprehensive, thoughtful and inclusive approach ensures your battery backup solution will support your current needs and adapt seamlessly to future demands and advancements.