The world has an insatiable need for data, which inevitably leads to increased energy usage and water wastage. Keeping up with digital demand while balancing sustainability is a major challenge, Steve Dawson, Closed Systems Manager, Guardian Water Treatment, discusses.
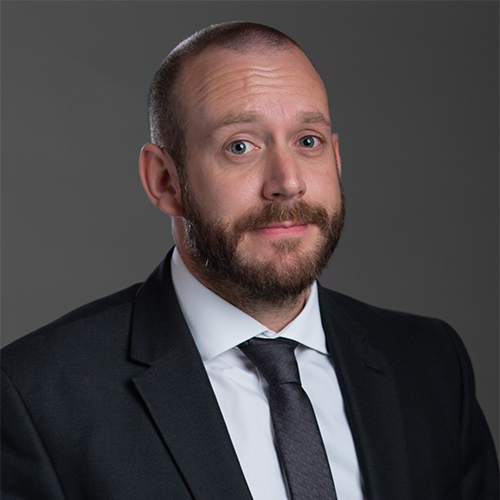
A fundamental part of ensuring data centres remain operational is cooling, which requires vast amounts of energy – 40% of the power used for facility operations goes towards this task. Part of the cooling process inevitably uses water. According to NPR reports, the average data centre needs 300,000 gallons of water a day to ensure optimum temperatures – equivalent to the water used in 100,000 homes. In drought-stricken areas, this is a very real concern and as climate change progresses, may affect more people across the globe.
There are ways to reduce this volume, something that must become a priority as the demand for data centres inevitably increases. Bigger data centres tend to use cooling towers which consume the greatest amounts of water, but are far more energy efficient than air-based cooling systems; it can therefore seem like balancing these two resource demands is at odds.
Ways to save water
Modern data centres can be kept at the right temperature – a constant 20°C to 24°C to prevent servers from performing inefficiently and unreliably – while also focusing on reducing resource wastage.
Water recovery and recycling
As mentioned, cooling towers are a popular choice in our largest data centres. Water is an excellent heat transfer medium and therefore adiabatic cooling systems are one of the most efficient methods, using around 40% less electricity than air-cooled systems.
To reduce the volume of water wasted in cooling tower processes, water can be recovered and rainwater harvested. In fact, 70% of process water can be recycled, making this approach a very effective method of improving the sustainability of operations.
There are also significant cost-saving benefits to water recovery and recycling, particularly in the very largest of data centres. For every cubic metre of water recovered, £2 is saved. If we look at the stats from NPR, 300,000 gallons equates to just 1,135 cubic metres, a saving of £2,270 a day. Commonly, we see the initial outlay of a water recycling system paying for itself in less than six months.
The benefits don’t end there. Clean, debris-free water will enhance cooling system efficiency and prevent legionella risk. Using a combination of media filtration, ion exchange and membrane filtration, data centre water recycling systems often leave water cleaner than when it came out of the mains, removing solids, bacteria, algae and viruses.
Real-time monitoring
There is still a place for air-cooled data centres, and many of the smaller facilities rely on this method of temperature control. Water is also used in this process, usually within a closed-circuit system.
Both air and water can be monitored, providing real-time data on conditions that can impact operational certainty. For closed systems, monitoring is used primarily to track the parameters that can be indicators of corrosive conditions, such as dissolved oxygen, galvanic currents, temperature, pressure and pH.
If left unchecked, corrosion can lead to system fouling, which compromises efficiency, causes pipe pitting and leads to eventual leaks. Without monitoring, problems often remain unseen until it is too late, leaving data centres at risk of catastrophic failure. Real-time monitoring is good for preventing downtime, reducing expensive repairs and conserving energy, and it also has a part to play in water conservation.
In the past, closed-system HVAC was checked using sampling, which only represented a snapshot in time – a sample of water is sent to a laboratory and analysed, with results taking days if not weeks to return. This approach often leads to knee-jerk flushing, where huge volumes of water are forced down pipes to clean out the system.
Sampling is carried out after routine maintenance, for example, which will undoubtedly disrupt conditions. Real-time monitoring can show you if and when conditions return to in-specification levels, meaning that on many occasions, flushing is avoided. HVAC systems that aren’t monitored in this way are more likely to be flushed as a precautionary measure.
Overall, monitoring will lead to more efficient and effective maintenance and improved operational certainty, extending asset life. Maintenance can be better planned and corrosion can be stopped before it even starts. Over 10 years, 24/7 monitoring will save money across the board, reducing energy usage, water wastage and unnecessary site visits – the latest systems are accessible on any Internet-enabled device, with alerts sent to responsible parties if problems arise.
Improving the efficiency of our data centres should be a priority of our age. Data comes at a cost and while it is seemingly ‘invisible’ to most people, it has a very real footprint.
Understanding the parameters that cause corrosion
Effective corrosion prevention is about monitoring and understanding the relationship between a number of key parameters. These parameters are:
- Pressure: Preventing oxygen ingress is the key to corrosion control and this starts with keeping a system pressurised correctly and as airtight as possible. Changes in pressure often lead to air ingress, meaning oxygen is entering the system
- Oxygen: Oxygen causes corrosion directly and creates the right conditions for bacteria and other pathogens to thrive, which can lead to microbial-induced corrosion (MIC) and other contamination issues. Dissolved oxygen should be checked for (as well as system pressure)
- Conductivity: Conductivity is a measure of the electrical potential of a medium to pass an electrical current through water. This is the basis of the electro-chemical reaction of the corrosion process
- pH: Chemical or electro-chemical water conditioning can affect the pH (acidity or alkalinity) of the water. This parameter can be critical with certain materials and is a useful measure for general corrosion rate arrest. Higher pH levels can also deter some bacterial proliferation
- Temperature: High temperatures can increase the corrosion risk; low to medium temperatures can encourage the proliferation of bacteria
- Loss of flow and stagnancy: This can lead to stagnancy and encourage free-flowing bacteria into the sessile state thus increasing the biofilm formation risk. Stagnancy results in dissolved oxygen coming out of the solution and generating air pockets. Loss of flow can impact the efficacy of inhibitors and biocides