The battery which underpins any uninterruptible power supply (UPS) is a major consideration for any data centre owner or operator. Traditionally, the market has utilised valve-regulated lead-acid (VRLA) batteries to ensure power continuity and continuous operation of the IT equipment and services they support. However, there are challenges with this technology in terms of their operating life, environmental requirements and monitoring. In this article, Marc Garner, VP, Secure Power Division, Schneider Electric UK & Ireland tells us more.
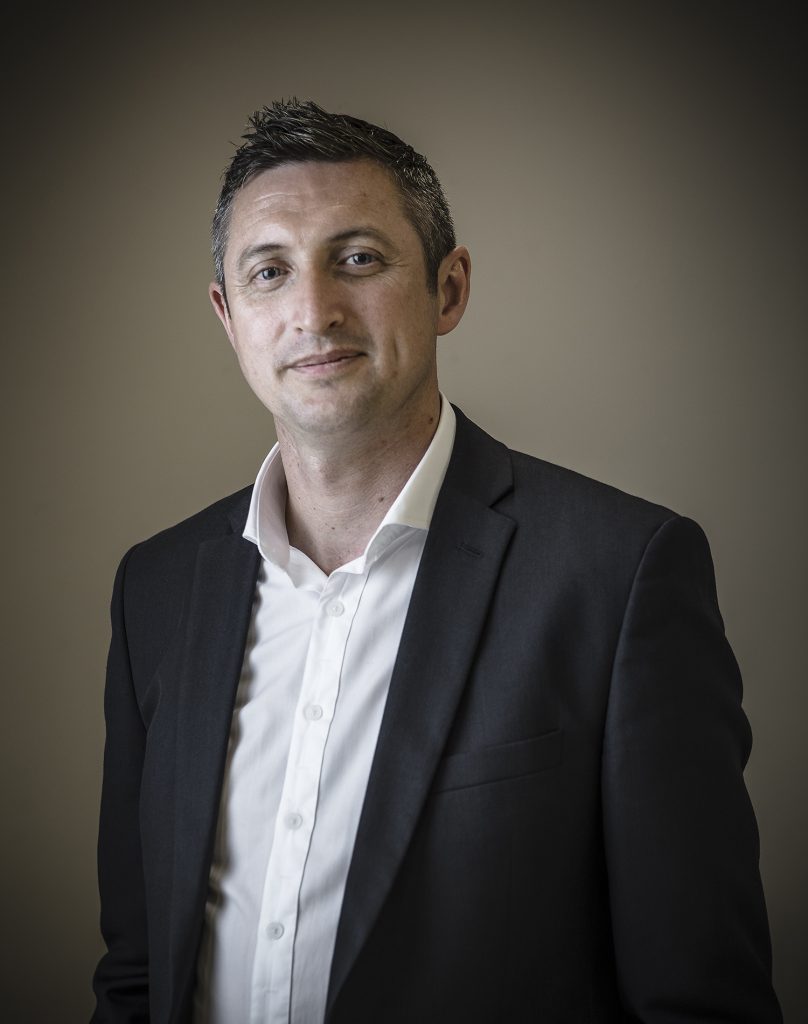
Lithium-ion (Li-ion) batteries have developed significantly since they were first introduced in 1985. The case for their use as a substitute for VRLA within data centre UPS has been well documented and has often centred on the reduced total cost of ownership (TCO) that is achievable over the battery’s lifecycle.
Apart from the business and technical trade-offs that must be considered, decision makers today must also address the issue of sustainability. Data centres are estimated to represent between 1-2% of global electricity consumption and when combined with the continued growth of data centre capacity, efficiency and sustainability have become more critical than ever.
It is, therefore, important to evaluate the environmental costs to be incurred by a wider adoption of Li-ion batteries at the expense of traditional lead-acid systems.
Raw materials
Any assessment of environmental impact must consider all parts of the product lifecycle, from raw material extraction through to disposal and/or recycling of component parts at the end of life.
As a mature battery technology, lead-acid cells are supported by a long-established recycling ecosystem designed to minimise waste and repurpose components. Plastic parts are recycled into more battery plastic; sulfuric acid is collected and resold as commodity acid; lead is smelted and returned to batteries or applied to other uses. One study suggests that lead-acid batteries have a return for recycling rate of 99.3%.
As a newer technology, Li-ion still relies mainly on mining extraction for raw materials as the necessary recycling practices are still being developed. However, when contrasting the two during the extraction process there are three main areas to consider.
Firstly, the toxicity of lead is hazardous to human well-being, and we have seen the elimination of lead in many aspects of our lives as safer alternatives become available. In contrast, Li-ion batteries contain less toxic material and are generally classified as non-hazardous.
Secondly, many of the questionable mining practices for Li-ion stem from the inclusion of the raw material cobalt which is often used in larger 3-phase UPS batteries. Cobalt is largely mined in the Democratic Republic of Congo and is not always regulated, and practices of unethical mining take place. It is therefore essential that UPS vendors only source batteries from manufacturers who are signed up tothe‘Responsible Minerals Initiative’ which ensures that companies adhere to ethical practices.
Thirdly, weight is another major aspect to consider, namely the mass of material required and the significant differences between the energy density of Li-ion compared to VRLA equivalents. A Li-ion battery can often be as little as a quarter the weight of lead-acid. Even considering the relative infancy of its supply chain-processes, the environmental impact of Li-ion batteries remains lower than VRLA.
Manufacturing and lifespan
The manufacturing process of VRLA batteries is also less complex than Li-ion and the conclusion is that the manufacture of a Li-ion battery has a greater environmental impact than a lead-acid alternative. The reality, however, is that this is a biased comparison, and true sustainability requires that the full lifecycle of both solutions be addressed, to gain an accurate understanding.
One feature of Li-ion cells is that they are more sensitive to external factors such as voltage and temperature and as such, cannot withstand the same level of variation of charging/discharging parameters. Consequently, they incorporate battery management circuitry, which can complicate the manufacturing process and increase the carbon footprint.
Although the components of the system are more complex, Li-ion batteries have a far longer lifespan and therefore require servicing and replacement less often than lead-acid systems. In fact, over a typical UPS lifecycle, VRLA cells require frequent replacement with the system replaced at least twice in 10 years.
For the data centre operator, a battery which does not meet the design requirement of the load presents a major risk to service continuity. The alternative is that operators will sometimes oversize the system, with all the environmental impacts present in manufacture, installation and operations.
By contrast, the characteristics of Li-ion cells means that none of this will apply to it over the same 10-year period – and the longer lifespan of a Li-ion battery is perhaps its major advantage in terms of sustainability and TCO.
Typically, lead-acid batteries are specified for service lives between three and five years whereas Li-ion models are specified for more than 10. This inherent improvement in sustainable performance is obvious given the associated Drop in costs from manufacturing to transportation and installation, as well as in operational expenses.
Installation and power consumption
While in use, the environmental impact of a battery can be attributed to the processes of installation and handling, energy consumption and length of service. The lighter weight of Li-ion means that individual batteries can be carried by hand rather than by a forklift, which also reduces the carbon footprint.
During its operational life, a Li-ion battery typically consumes less energy than a VRLA alternative because its internal chemistry makes for a slower self-discharge rate. As such, they do not need the same amount of recharging, and over its lifetime, a lead-acid battery will typically lose 0.2% of its rated capacity, roughly double that of a Li-ion battery which typically loses only 0.1%.
End of life and recycling processes
Despite its relative newness, a commitment to best practices with regards to taking back defective and end of life batteries is helping reduce the environmental impact of Li-ion, whilst its recycling processes continue to be established and mature. There is, for example, already an industry advancing to provide these services.
At the same time, we’re seeing the electric vehicle market paving the way for second use applications and a study by the National Renewable Energy Laboratory identified that when EV batteries reach the end of life, a promising second use is to “replace grid-connected combustion turbine peaker plants and provide peakshaving services.
In addition, examples of niche markets utilising Li-ion cells for second use include microgrid applications, and hospitals to support emergency lighting.Established pyrometallurgical techniques are also being applied to Li-ion batteries at end of life and provide a simple and efficient means of recovering valuable cobalt and nickel elements. Newer Hydrometallurgical techniques that use water as a solvent to extract and recover valuable elements also promise to recover more than 95% of all constituent materials.
Looking forward
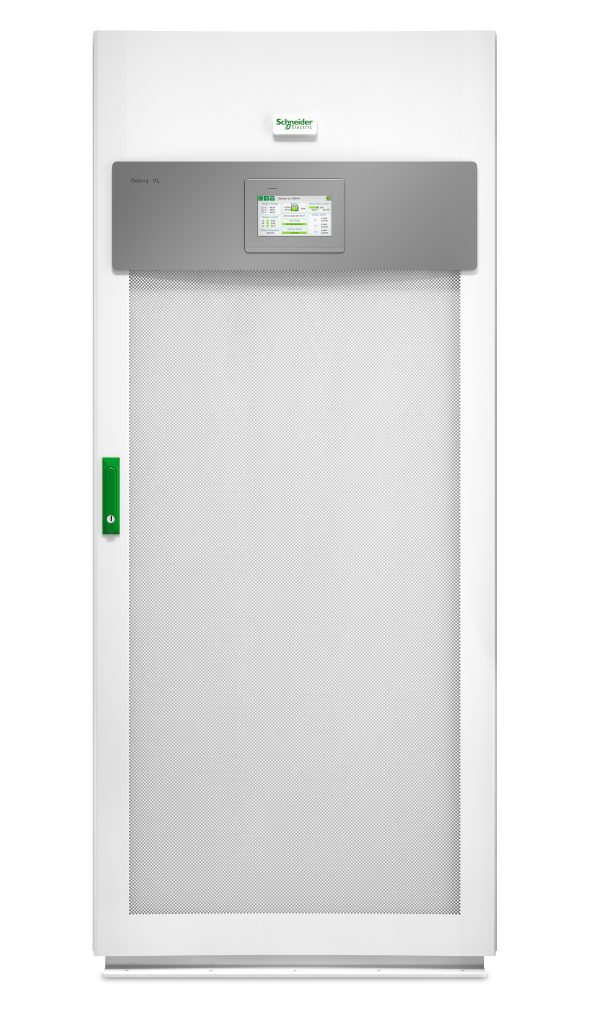
Although there are inevitable environmental impacts emerging with the growth of this resilient and energy efficient technology, when evaluated holistically, it’s clear that Li-ion batteries offer a more sustainable solution for UPS systems.
When combined with the characteristics of more compact design, lighter weight, longer lifecycle, and more reliable performance, they make a compelling case for use in an industry where both space and uptime are at a premium.
Given the innovation in battery manufacturing and recycling, and with many techniques already advancing, we believe Li-ion batteries will continue to provide a safe, cost effective, and resilient power solution for the sustainable data centres of the future.
You can learn more about the sustainability impact of Lithium-ion batteries in Schneider Electric white paper #71 – download here.